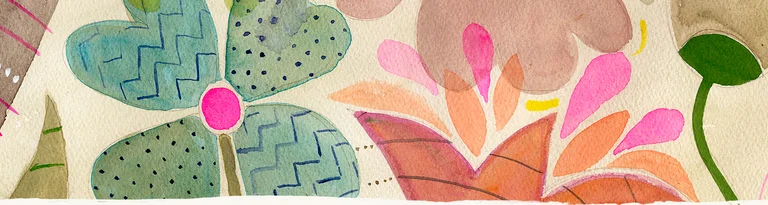
Manufacturing
We regularly visit and inspect our factories and inspections are also carried out by independent third-party organisations. Every stage of the garment manufacturing process, from weaving to stitching, builds on genuine skills, knowledge and experience. We are inspired by the passion and drive found in the textile industry and are continually developing new ideas and creative solutions in close collaborative partnerships with producers.
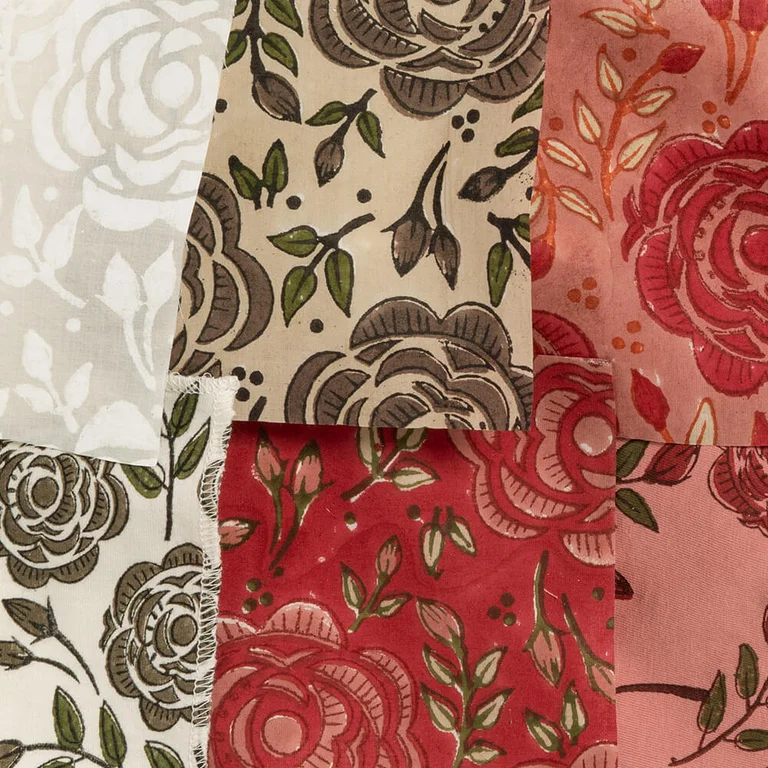
Printing methods
Prints of every kind have become our signature. Watercolour designs are converted into data files and then printed using digital, rotary and automatic screen printing techniques.
We alsouse manual printing techniques performed
with blocks and screens, for example.
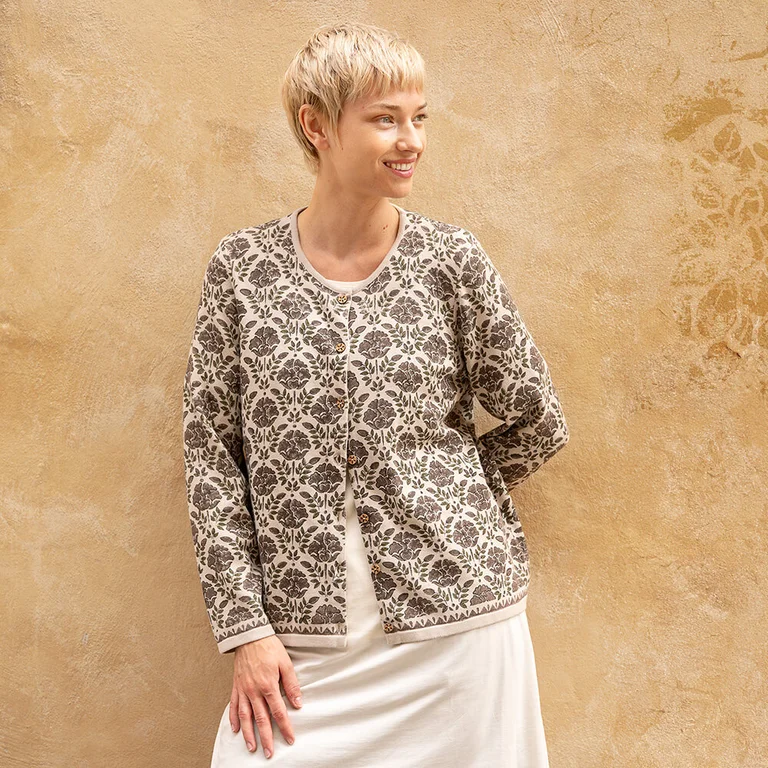
Woodblock printing
Block printing is a centuries-old craft that produces beautiful patterns on textiles and paper.
The technique was used in Japan and Korea as early as the 8th century to embellish religious manuscripts, and in Europe it was the first method of printing on paper. It was developed by Johannes Gutenberg in the 1440s as he worked on his idea for a printing press to produce books.
We’ve been working with block-printed designs here at Gudrun Sjödén since the 90s to celebrate and support this traditional craft. Skilled artisans carve patterns into the surfaces of blocks made from dense, durable wood, like Indian rosewood. A separate block is used for each colour. The printing is done entirely by hand, with each block first dipped into a dye paste and then pressed, with great precision, onto the fabric, creating the pattern metre by metre. This transforms the fabric into a palette of patterns, shapes and colours.
Many of our products are printed in Jaipur, India, where block printing is a deeply rooted art form. Tremendous skill and long experience are required, as each block has to be carefully lined up by eye and then pressed steadily onto the fabric. For this reason, it inevitably takes much longer to produce block-printed than machine-printed fabrics. Each product is unique and beautiful, crafted with care and patience – a far cry from mass production.
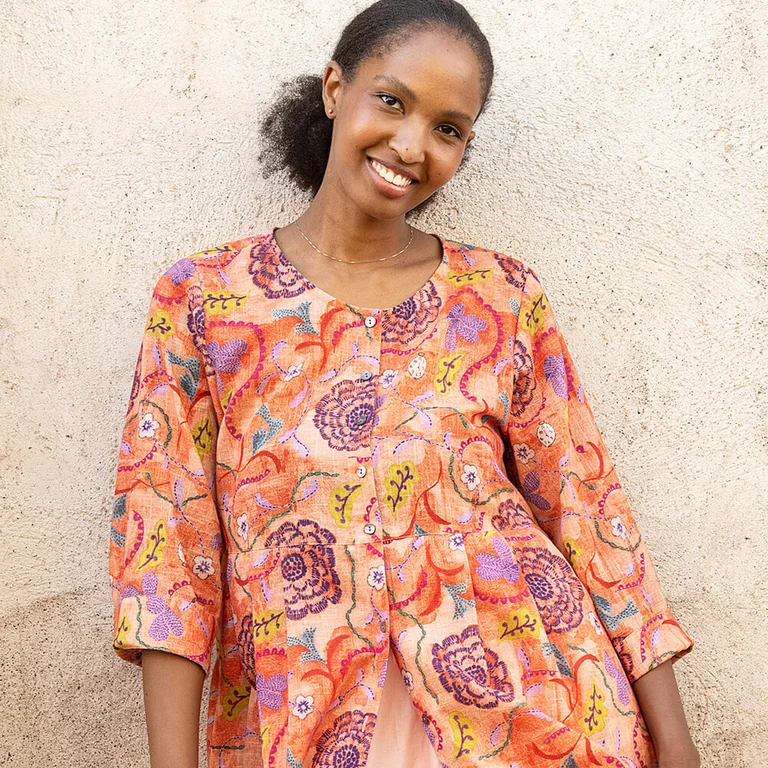
Digital printing
Digital textile printing is an innovative process that combines technology and creativity to produce detailed and colourful designs on fabrics.
Unlike traditional printing methods, digital printing uses neither stencils nor blocks, making it an efficient and versatile process.
The design is transferred directly from a digital file to the fabric, which ensures extreme precision and means it can be customised to bespoke needs. This technology opens new avenues for creativity, allowing intricate details and a wide colour palette to come to life in a way that was previously difficult to achieve.
Digital printing is also highly efficient as the process applies inks in precise amounts and uses minimal amounts of water. By reducing ink waste and resource usage, the technology optimises both the production process and the design quality.
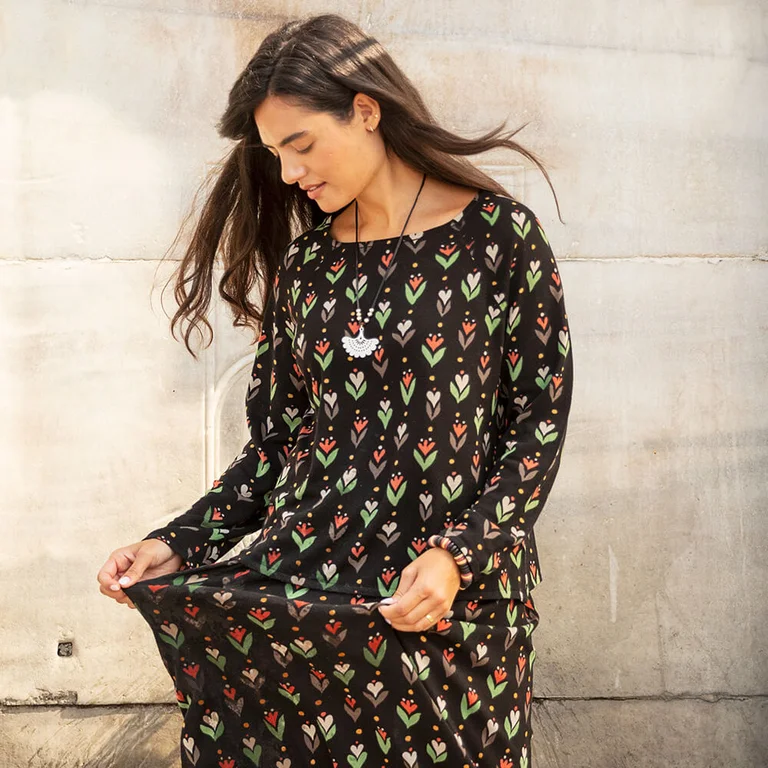
Screen printingScreen printing is a traditional printmaking technique that creates sharp-edged and detailed patterns on textiles.
It involves pushing ink through a fine mesh that is stretched over a frame. The printed design is produced using a stencil on the screen, which is how it gets its name. Each colour requires a separate screen and stencil. So five frames are needed for a five-colour print.
Some garments and accessories, such as our knitwear, are hand screen-printed, which is a meticulous and artisanal process. The garment, which is sewn together except along the sides, is laid flat on a long printing table. Large scrapers are then used to draw the ink manually through the stencil and transfer the pattern to the fabric. The frame is then lifted and moved to the next garment, and the process is repeated for each colour.
It is a method that requires strength, precision and exceptional craftsmanship. The result is a design that is rich with vibrant colour and each garment displays distinct traces of the artisan’s work. No fabric is wasted using this method, because the garment being printed is already finished. Not like when a fabric is printed and then the
pattern is cut out.
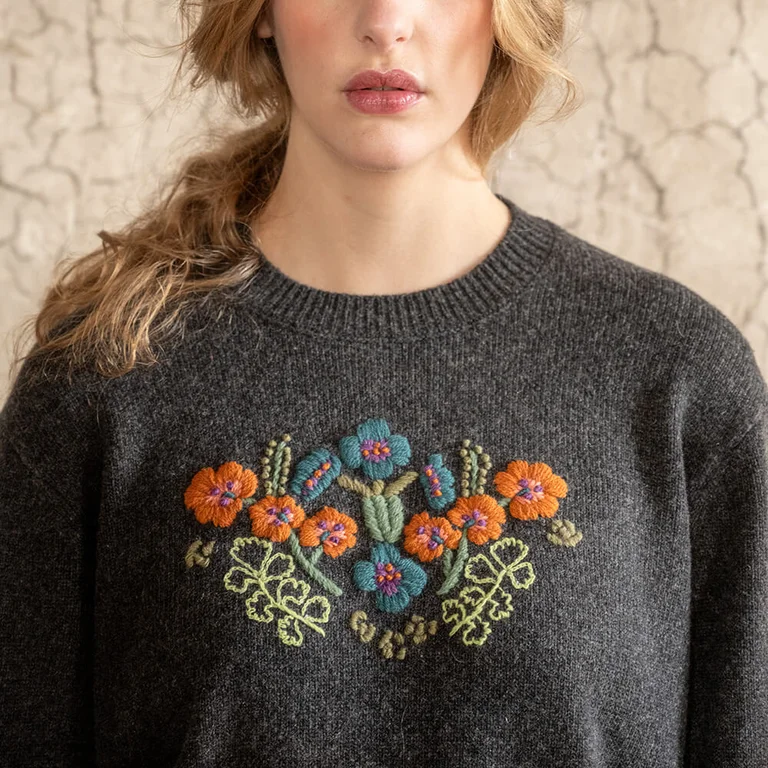
Embroidery techniquesEmbroidery has the power to turn even the simplest fabrics into one-of-a-kind creations. You will find it on our tablecloths, cushions, clothes and accessories – everywhere, in fact.
Many of our creations and accessories feature hand embroidery, a traditional craft passed down through generations of artisans who put their heart and soul into every stitch. Machine embroidery is a modern technique that produces results in less time. It is not as detailed as hand embroidery, but still requires skill and precision.
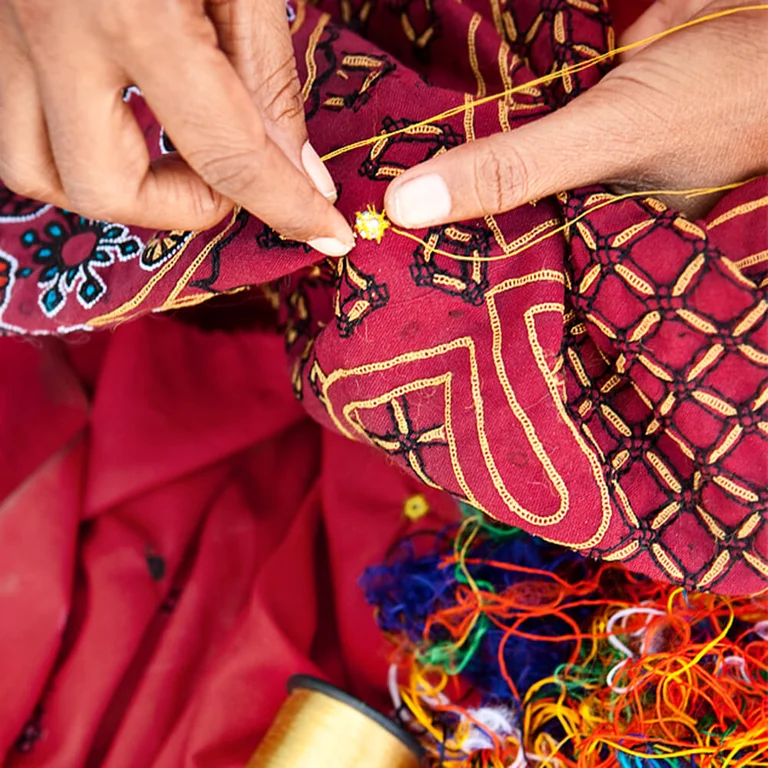
Hand embroideryHand embroidery is a deeply rooted art form in North India, especially in the regions around Jaipur, New Delhi and Lucknow, where some of the most intricate and traditional techniques are practised.
Our skilled suppliers introduce us to the most complex and varied embroidery methods. Every town or village often specialises in a unique technique, such as Chikankari, kantha (a simple running stitch), herringbone stitch, chain stitch, beaded or mirror embroidery.
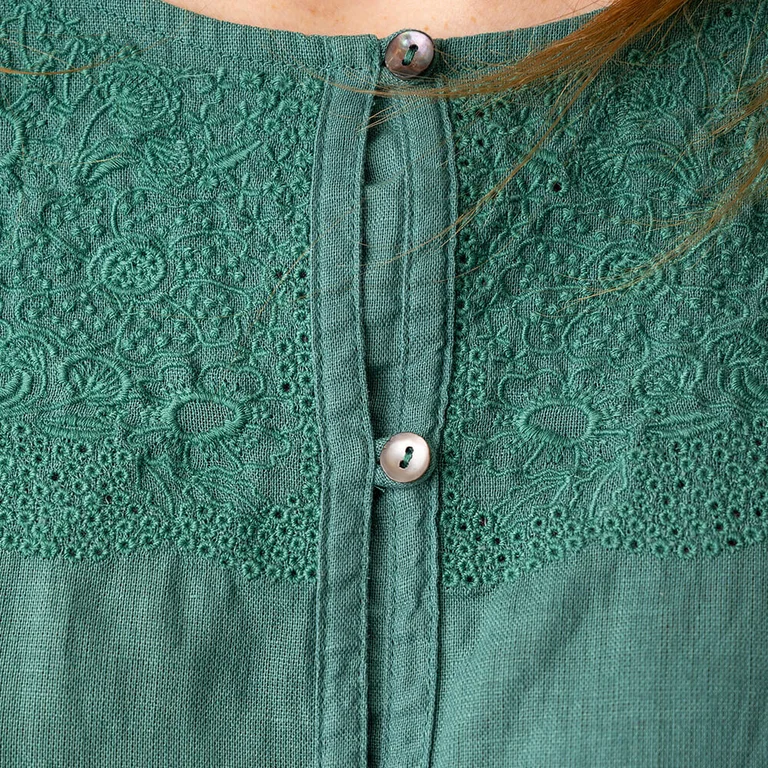
Machine embroideryWhile hand embroidery offers unparalleled artistry, machine embroidery enables the production of large quantities with greater speed and extreme precision.
Although machines do the actual stitching, human expertise and knowledge are crucial in designing the technical drawings that control the equipment.
The two main types of embroidery machines are Schiffli and multi head. Schiffli machines use a single colour with multiple parallel needles embroidering several metres of fabric at a time. This technique is efficient but has limitations in the complexity of designs it can produce.
Multi head is a very versatile machine embroidery technique and therefore most widely used. It has the ability to handle multiple colours simultaneously, allowing for more intricate and elaborate designs. Considerable expertise is required to program a multi head machine, as each colour and section of the design must be meticulously programmed. To avoid time-consuming manual work afterwards, it is crucial to minimise ‘jumps’ – when the needles move from one part of the design to another. Once the machine is correctly set up, the fabric is stretched and fixed in a frame to ensure it stays in place during the embroidery process.
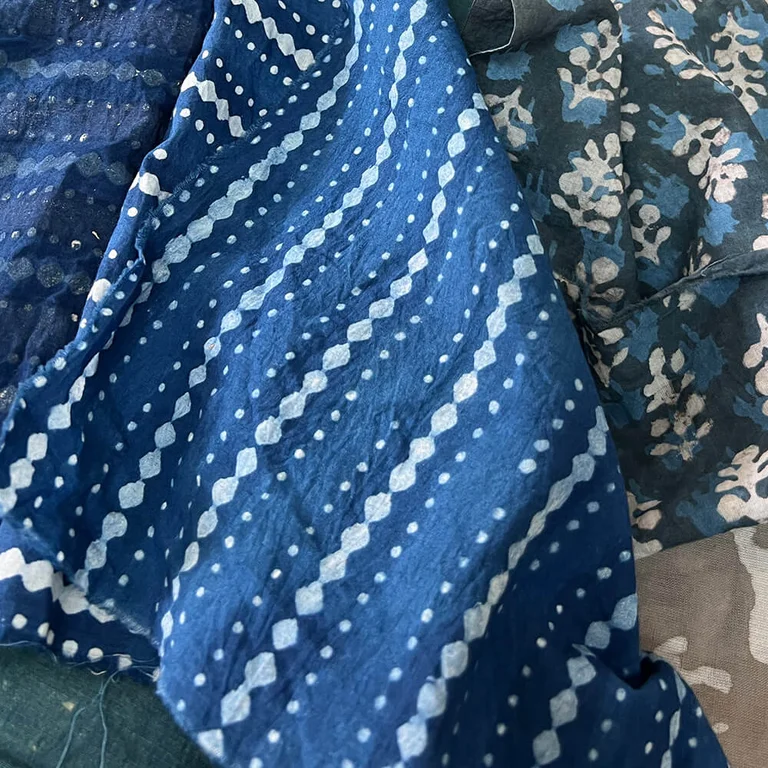
Textile waterproofingOur waterproof garments are coated with a water-repellent finish from RUDOLF GROUP. The water-repellent coating, BIONIC-FINISH® ECO - RUDOLF is environmentally-friendly and biodegradable.
The product is free from harmful chemicals, such as fluorocarbons, formaldehyde and paraffin.
The inside of our cotton parkas and coats are coated with Rudolf Ruco-Guard WR. Our rain jackets are finished with a TPU (thermoplastic polyurethane) coating. TPU can be recycled and is non-toxic.
We do not accept packaging with silica gel, which contains the chemical DMF (dimethyl fumarate), and we do not use moth repellent agents or flame retardant chemicals on any of our products.
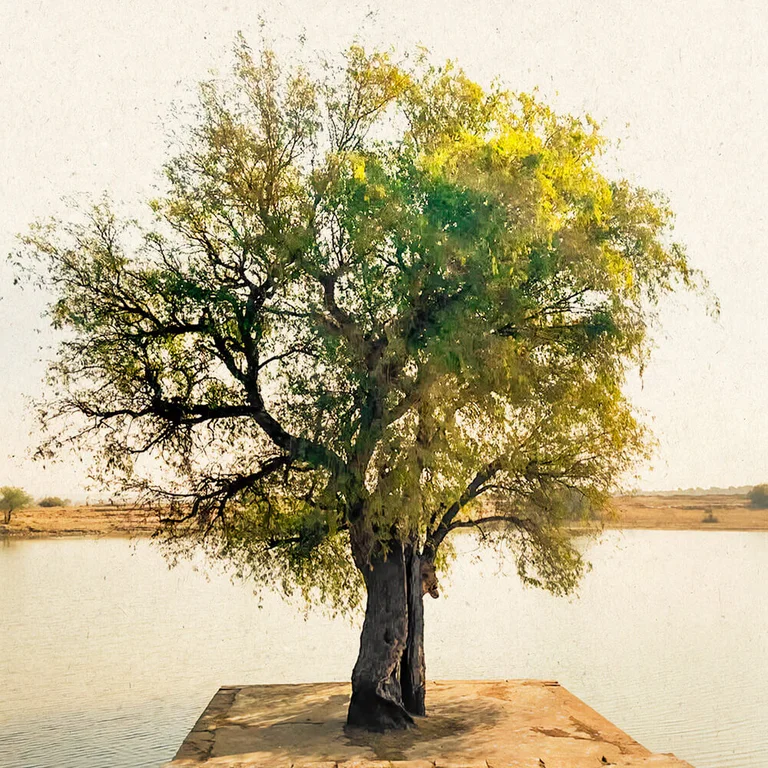
Production countriesIndia, Bulgaria, China, Portugal, Greece, Italy, Marocco and Nepal. Many of our products are made in India.
There is a deep respect for raw materials, ancient craft traditions and dyeing techniques in India – a source of inspiration for us at Gudrun Sjödén. We build long-term collaborative relationships with family-owned companies and prefer to work closely with a handful of suppliers that understand our concept and are adept at interpreting our designs.
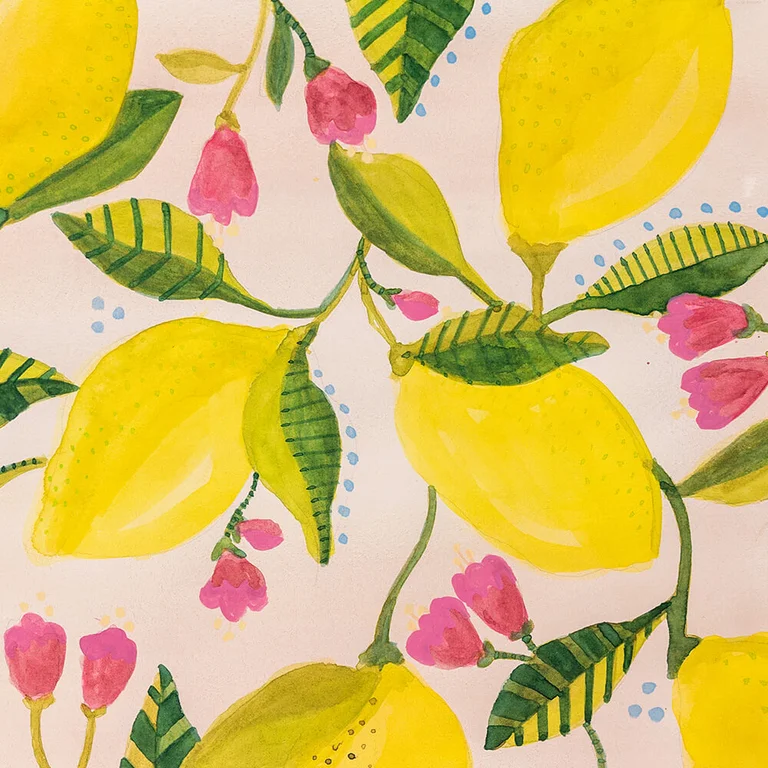
Code of ConductWe have been actively working with a Code of Conduct with our suppliers since 2001.
We believe that long-term relationships with suppliers is the most productive way to address these issues.
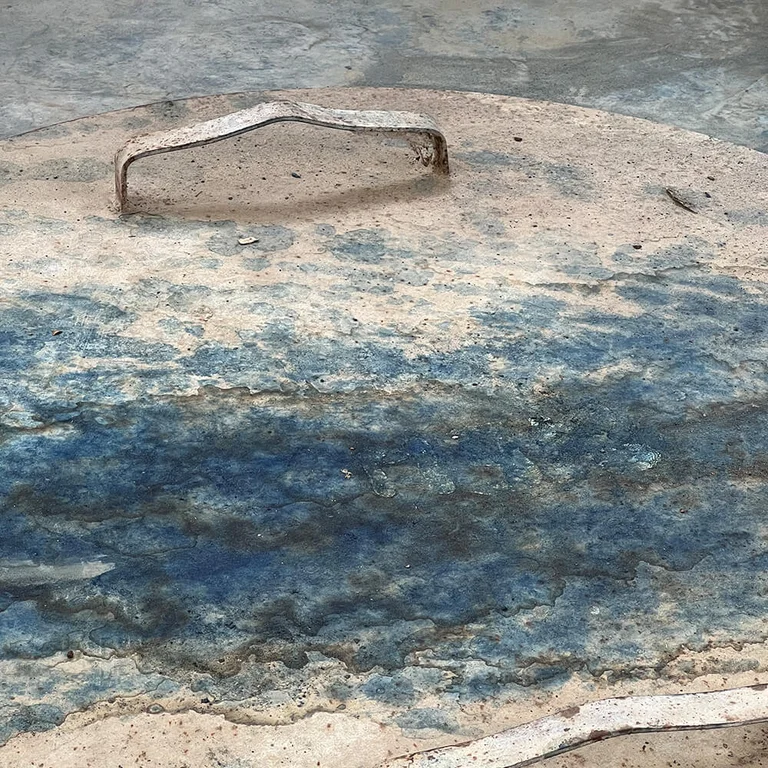
Chemical treatmentsOn the reverse of our water-repellent outerwear, we use a PU coating, which is a protective film made of polyurethane.
Although the coating is not harmful in itself, the production of PU polymers involves the use of isocyanates and alkane diols, which are hazardous substances. Appropriate safety measures are therefore taken in the manufacturing facilities to protect the health of the workers.
Our waxed tablecloths are coated with acrylic, a safe polymer. The manufacturer of the acrylic is an Oeko-Tex® certified company and the coating has been approved by multiple large companies for use in baby products, which means it is safe for use on bibs and tablecloths.
We do not accept packaging with silica gel, which contains the chemical DMF (dimethyl fumarate), and we do not use moth repellent agents or flame retardant chemicals on any of our products.
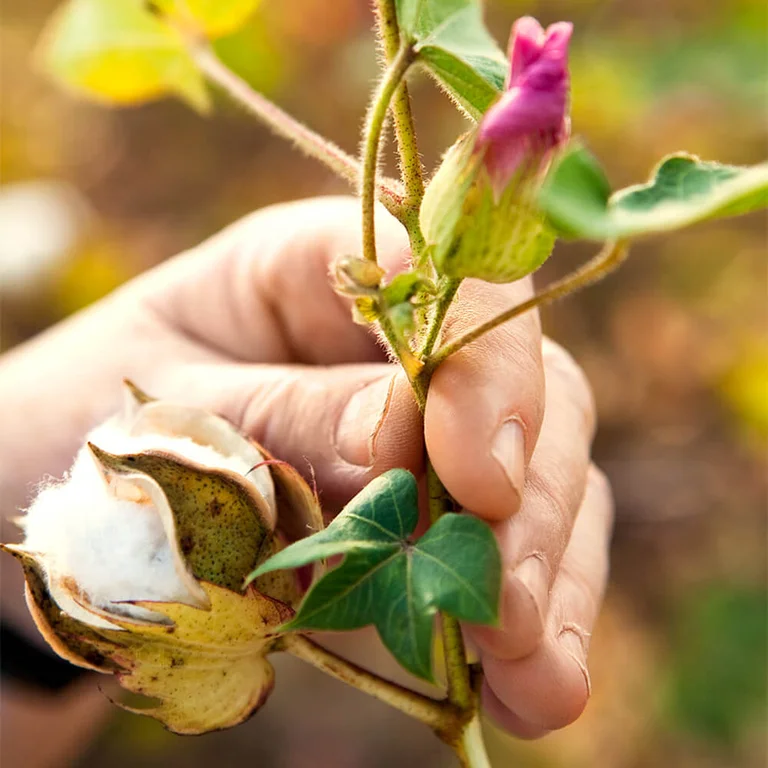
Amfori BSCI/SA80000We have been a member of the Business Social Compliance Initiative (Amfori BSCI) since 2007.
Members of the organisation adhere to a common Code of Conduct. The factories are regularly audited by independent third parties to ensure ongoing compliance. Our production facilities in risk countries (Bulgaria, Marocco, China and India) comply with Amfori BSCI’s guidelines. This process helps us to improve working conditions and protect human rights in the regions where we operate.
Further details can be found at
www.amfori.org/content/amfori-bsci
We also accept certification of social accountability endorsed by SA 8000, SMETA and other standards.
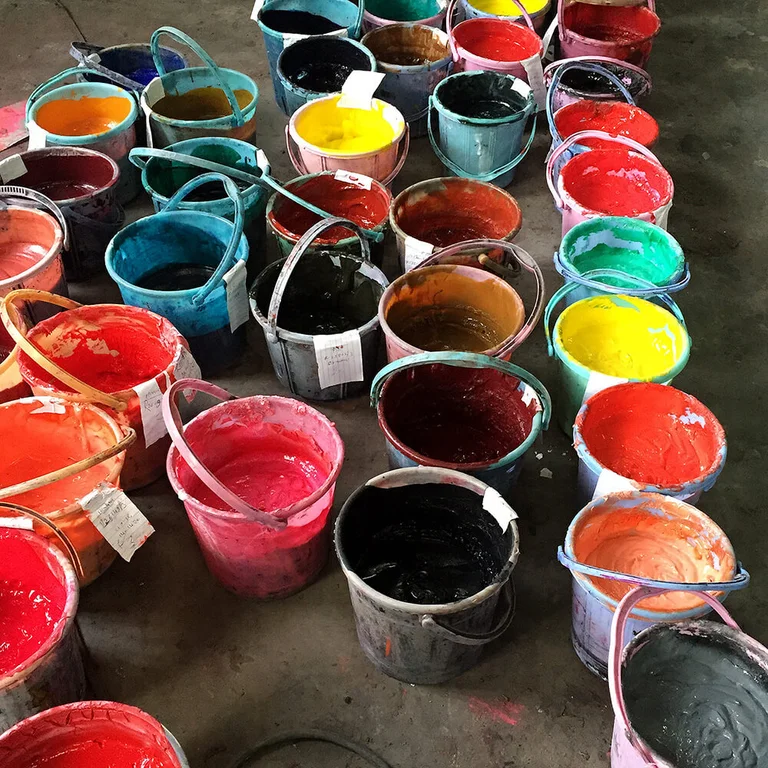
REACHRegistration, Evaluation, Authorisation and Restriction of Chemicals – REACH.
The European Chemicals Agency (ECHA) is responsible for the REACH regulations that aim to ensure safe use of chemical substances and protect human health and the environment in the EU. Chemicals are used at the textile dyeing and post-processing stages, such as softening and dirt-repellent treatments.
Chemical substances of very high concern are included in a so-called Candidate List, and if a substance is on the list, or if goods contain any of the substances, this must be registered within six months.
All of our suppliers undertake to comply with the REACH regulations and we conduct independent tests to ensure compliance. We are also a member of the Chemicals Group, which keeps us updated on the latest REACH requirements and other chemical-related matters.